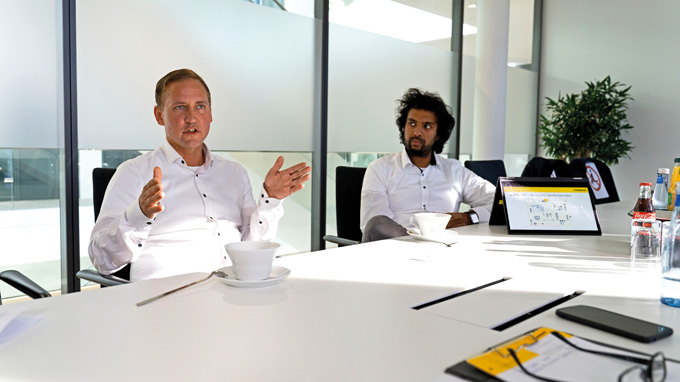
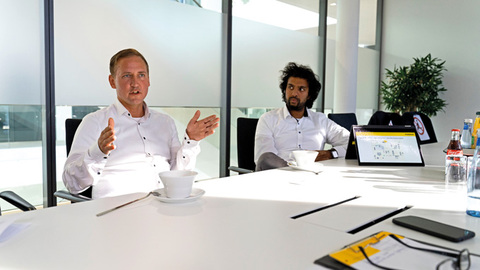
Aurel Buda und Sai Seidel-Sridhavan sind davon überzeugt, das SPE seinen Platz finden wird als Ergänzung der heute verfügbaren Technologien
IO-Link unlimited
Als Spezialist für smarte Sensorik bringt Turck Intelligenz an die Maschine und schafft so die Verbindung zu Industrie 4.0 und IIoT. Welche Rolle dabei IO-Link als Basistechnologie im Portfolio spielt und welche weiteren Entwicklungen bei dieser Technologie zu erwarten sind, erörtern Turcks Produkt Marketing Manager Sai Seidel-Sridhavan und Aurel Buda, Leiter Produktmanagement Fabrikautomation Systeme, im Gespräch mit Andreas Gees vom Fachmagazin elektroAutomation.
IO-Link hat gerade mit den Konzepten für das IIoT an Bedeutung gewonnen. Welche Rolle spielt diese Kommunikationstechnik für Turck?
Seidel-Sridhavan: Als Gründungsmitglied der IO-Link-Community haben wir immer gemeinsam mit unseren Kunden das Ziel verfolgt, die digitale Kommunikation vom Steuerungslevel bis zum letzten Meter in der Maschine zu realisieren. Damals haben wir in eine Technologie investiert, deren Entwicklung wir anfangs nicht absehen konnten. Heute ist IO-Link ein wichtiger Part in unserer Unternehmensstrategie. Jedes Sensor- und Kommunikationsprodukt, das wir für die Fabrikautomation entwickeln, ist zumindest in einer IO-Link-Version verfügbar. Oft fällt die Entscheidung für IO-Link strategisch und es werden zuerst IO-Link-Geräte herausgebracht. Neben RFID ist IO-Link eine unserer zwei Kerntechnologien für digitale Daten aus der Maschine und deren Einsatz in der Automatisierung. IO-Link ist zuerst eine Schnittstelle zwischen Sensor und Steuerung, sie bietet aber auch die Basis, um IIoT-Konzepte zu realisieren.
Buda: Turck produziert nicht nur eine große Zahl von Sensoren verschiedener Art für Steuerungsaufgaben oder das Prozessmonitoring, sondern vieles mehr für umfassende IIoT-Lösungen. Unseren Kunden bieten wir das komplette IO-Link-Portfolio, von der Sensorik über RFID-Schreib-Lesegeräte, Netzteile und Leuchten bis hin zu Hubs und Mastern für I/O-Systeme und -Blockmodule – quasi vom Sensor bis zur Cloud. Ergänzt wird das alles durch smarte Softwareangebote, die Anwendern den Einsatz der Technologie deutlich erleichtern. Wir sehen IO-Link als die Schnittstelle zwischen der Steuerungs- und der IIoT-Welt und beschäftigen uns deshalb auch intensiv mit Condition Monitoring.
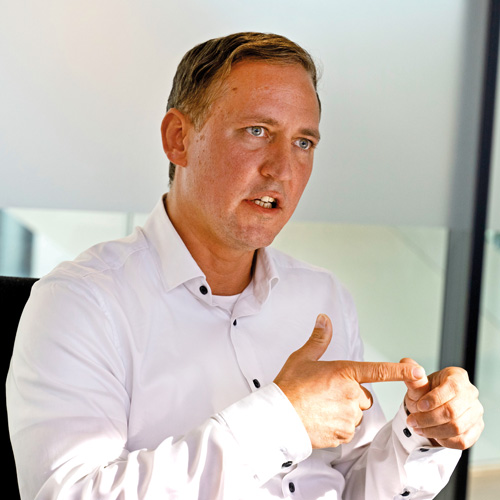
IO-Link hatte anfangs Akzeptanzprobleme. Das hat sich geändert. Warum hat Turck ein so umfangreiches Portfolio an Geräten mit IO-Link entwickelt?
Buda: Die effiziente Vernetzung auch einfacher Schalter in einer Maschine und damit die bidirektionale Kommunikation in die Feldebene ist ein bedeutender Use Case bei Turck. IO-Link ist offen und feldbusunabhängig. Das unterstützen wir auch mit unserer Ethernet-Multiprotokoll-Strategie in den Mastern. Die Palette der Sensoren reicht vom einfachen Näherungsschalter bis hin zu komplexen Geräten, die zusätzliche Informationen über ihren Betriebszustand sowie die Umgebungsbedingen liefern. Unsere Radarsensoren etwa unterstützen Condition Monitoring mit integrierten Analysen von Luftfeuchtigkeit, Vibration, Temperatur etc. Mit IO-Link bewegt sich Turck in einem Ökosystem, in dem auch standardisierte Aktorlösungen anderer Hersteller verfügbar sind. Deshalb haben wir uns auf der I/O-Geräte-Seite auf Aktorik eingestellt. Wir binden I/Os über IO-Link an den Master an, um so einfache Sensorsignale einzusammeln, aber auch mit höheren Strömen Ventile zu schalten.
Seidel-Sridhavan: Die Akzeptanz ist mit der zunehmenden Verfügbarkeit IO-Link-fähiger Aktorik gewachsen und viele Gerätehersteller haben diese Schnittstelle für sich entdeckt. Anfangs haben Condition Monitoring und IIoT zwar Interesse geweckt, doch das Ökosystem war nicht komplett. Heute reden wir über ein breites Ökosystem von Sensoren, Ventilinseln oder Stromversorgungen. Es hat sich herauskristallisiert, dass IO-Link eben nicht nur für Sensoren, I/Os und Steuerungen relevant ist. Hersteller sparen sich die Integration unterschiedlicher Schnittstellen. Anwender profitieren von dieser einzigen Schnittstelle, mit identischen Leitungen, Steckverbindern und Software.
IO-Link hat an Akzeptanz gewonnen, als erste Konzepte zum IIoT aufkamen. Früher wurde IO-Link zum Konfigurieren von Sensoren genutzt.
Buda: IIoT, Condition Monitoring, Predictive Maintenance, Prozessoptimierung und Asset Management haben IO-Link beflügelt. Schon immer war unsere Botschaft, dass IO-Link auch eine kostengünstige Infrastruktur erlaubt. IO-Link kommuniziert über eine preiswerte Standard-Leitung. Obwohl sich Ventilinseln oder Hubs auch mittels Industrial Ethernet vernetzen lassen, sind dabei die Kosten deutlich höher, während die Kosten eines Sensors durch die Integration von IO-Link nicht gestiegen sind. Und die Übertragung von Prozess-, Identifikations- und Zugangsdaten bildet letztlich die Basis für Digitale Zwillinge und Asset Management.
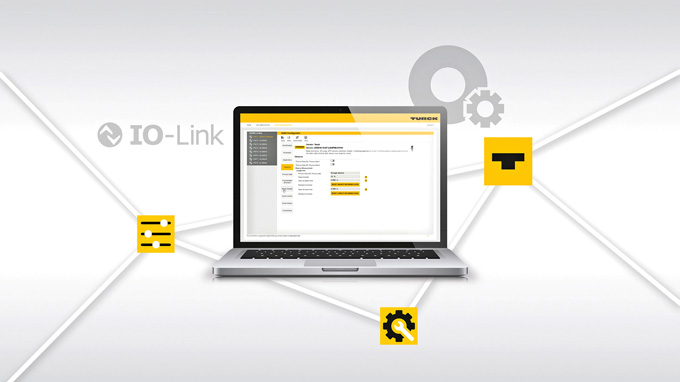
Turck bietet Lösungen vom Sensor bis in die Cloud. Welche IO-Link-Softwarevarianten kommen zum Einsatz, um Konfiguration und Betrieb zu unterstützen?
Seidel-Sridhavan: Die Konfiguration in Profinet-Steuerungen realisieren wir heute direkt in dieser, wobei die Daten der IO-Link-Konfiguration in die Profinet-GSDML-Datei des Masters integriert werden. So kann der Anwender im gewohnten Engineering-System für die Steuerungswelt auch seine Komponenten konfigurieren. In die Webserver unserer Komponenten haben wir darüber hinaus ein Tool integriert, das den Zugriff auf den IODD-Finder ermöglicht, eine globale Datenbank fast aller IO-Link-Devices im Markt. Die IO-Link-Device-Description steht dann im Engineering-System oder in einem Konfigurations-System über automatisierte Schnittstellen zur Verfügung.
Buda: Unser webbasiertes Konfigurations-Tool hat dieselbe Oberfläche, um automatisch die IODDs aus dem Netz zu laden. Das Tool eignet sich zum Konfigurieren, aber auch für die Erstinbetriebnahme. Das betrifft beispielsweise auch die RFID-Schreib-Lesegeräte, bei denen die Konfiguration mittels IO-Link sehr einfach ist. Ergänzend dazu können wir auch Web-Apps programmieren, die beispielsweise das Einmessen von Sensorik erleichtern. Das haben wir für unsere Radar-, aber auch für unsere Vibrations-Sensoren realisiert, und wir bauen das Angebot kontinuierlich aus. IO-Link-Profile definieren darüber hinaus das standardisierte Verhalten einzelner Geräte oder Klassen. Es gibt schon einige Profile, beispielsweise für smarte Sensoren. Damit können herstellerunabhängig Geräte gleichen Typs softwaremäßig auch gleich behandelt werden.
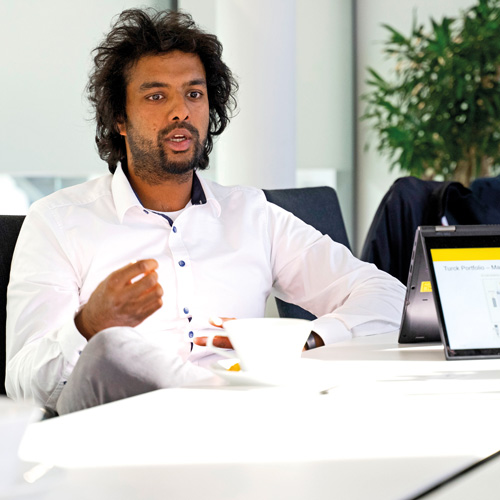
Welche Bedeutung hat IO-Link für Condition Monitoring und Predictive Maintenance?
Seidel-Sridhavan: Die klassische Automatisierungs-Struktur sieht eine Verbindung zu einer SPS vor. Von da aus gehen die Daten beispielsweise an MES-Systeme. Doch unterschiedliche Kundengruppen fordern zunehmend den parallelen Zugriff direkt auf die Daten aus den IO-Link-Mastern. Über die Lebenszeit einer Anlage lässt sich das Condition-Monitoring-System so beliebig erweitern oder modifizieren. So eine parallele Schnittstelle bieten wir in unseren Mastern seit vielen Jahren. Sie ermöglicht es, Condition Monitoring mittels unserer Edge Gateways sowie geeigneter Cloud Services zu realisieren. Unser Konzept der dezentralen Automatisierung beinhaltet nicht nur die Komponenten außerhalb des Schaltschranks in IP67, sondern auch die Datenvorverarbeitung direkt an der Maschine. Dazu bieten wir zu unserem Edge Controller auch Logik-Funktionen. Wir sind auch offen für Industriestandards wie OPC UA und MQTT, um in die IT-Ebene zu kommunizieren.
Buda: Als die Themen IIoT und Industrie 4.0 aufkamen, war viel von Big Data die Rede, um später Machine-Learning-Projekte zu starten. Doch viele Daten erzeugen viel Traffic und benötigen viel Bandbreite und Speicherplatz. Heute ist es üblich, nur smarte Daten zu übertragen. Das kann eine Bewertung der Date oder ihrer Änderungen sein, es kann auch eine Datenaggregation sein oder die Bewertung von Zusammenhängen zwischen verschiedenen Sensorwerten. Hinzu kommt der Aspekt der Latenz. Werden Entscheidungen direkt auf dezentralen Edge Controllern getroffen, ist eine schnelle Reaktionszeit sichergestellt.
So bietet sich IO-Link als Basis für Digital Services an?
Buda: Unsere Edge Controller bilden die Plattform, um die Daten mittels Logik vorzuverarbeiten oder über Protokolle wie OPC UA zu visualisieren beziehungs-weise in die Cloud zu senden. Dafür bieten wir vorgefertigte Funktionsblöcke und Module. Unsere Global Application Engineers und Sales Teams besprechen mit dem Kunden die Aufgabenstellung und realisieren ein Proof of Concept. Oft geht dies bis zur Visualisierung. Häufig geht es aber auch darum, an MES- oder Cloud-Systeme anzudocken. Wir arbeiten dazu auch mit Systemintegratoren zusammen, die Applikationen schlüsselfertig programmieren. Unsere Geräte können mit beliebigen Systemen kommunizieren, aber wir bieten auch eine eigene Cloud mit dem Motto ‚Konfigurieren statt Programmieren‘. Zielgruppe sind diejenigen Maschinenbauer, die sich mit Digital Services kaum auskennen. Diese beginnen mit Remote Access und mit Turcks Cloud Service können sie alle Daten visualisieren, speichern und auswerten. Am Ende stehen schlüsselfertige Lösungen, die adaptierbar sind.
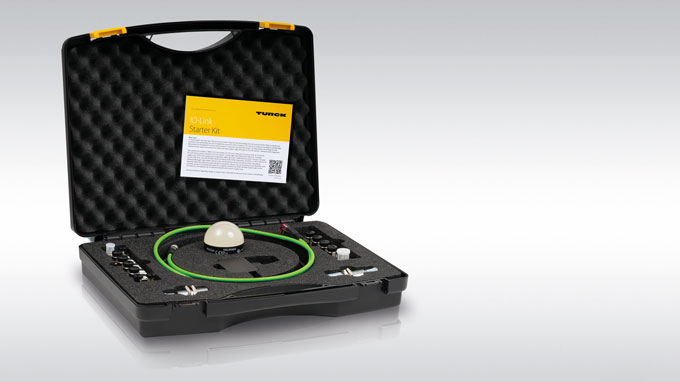
Wie beurteilen Sie die aktuellen Entwicklungen zu IO-Link+ oder IO-Link over Single Pair Ethernet?
Buda: Die Ursprünge von Single Pair Ethernet kommen aus der Automobilindustrie, um den CAN-Bus abzulösen. Bei SPE haben sich verschiedene Standards herauskristallisiert, die Übertragungslängen und Datenraten definieren, die auch für den Einsatz in der Automatisierung und in der Prozessindustrie geeignet sind. Auch wir in der IO-Link-Community haben uns die Entwicklungen genau angeschaut und die Technologie mit 10 Mbit über längere Distanzen als IO-Link+ spezifiziert. Obwohl es sich um ein anderes Übertragungsmedium handelt, wollen wir die Vorteile von IO-Link beibehalten. Wir suchen keinen Wettbewerb zu Profinet, Ethernet IP oder anderen Ethernet-Protokollen. IO-Link+ ist vielmehr für Geräteklassen gedacht, die wir heute nicht bedienen können. IO Link ist limitiert auf 20 Meter zwischen Master und Gerät. Hinzu kommt die Datenrate von unter 1 Mbit. Mit dem Aufkommen von IIoT-Konzepten werden häufig mehr Daten fließen. Auch kann IO-Link heute nicht in der Prozessautomatisierung genutzt werden. IO-Link+ legt den Grundstock, um Daten bis Zone 0 und 1 übertragen zu können.
SPE und Protokolle wie Profinet könnten sich durchaus zur Alternative zu IO-Link entwickeln. Was sind die Unterschiede und wo liegen die Grenzen?
Buda: Eine der Erwartungen an SPE ist, Sensoranschaltungen zu vergleichbaren Kosten wie bei IO-Link zu ermöglichen, was nach aktueller Einschätzung sehr unwahrscheinlich ist. Auch wird es kaum möglich sein, Sensoren über lange Distanzen und ungeschirmte Leitungen anzuschließen. In der Profinet-Community wird ein Kostenvorteil vor allem in den ungeschirmten Zweidraht-Leitungen gesehen. Eine so robuste Kommunikation wie bei IO-Link dürfte es deshalb mit SPE kaum geben. Auch auf der Geräteseite besteht ein Unterschied. Es gibt komplexe Sensoren, bei denen die Kommunikationsschnittstelle keinen wesentlichen Anteil an den Gesamtkosten verursacht. Hier dürfte SPE schneller zum Einsatz kommen. Bei einem simplen Sensor wird sich IO-Link als feldbusunabhängige Lösung behaupten. Ein IO-Link-Master hat heute vier oder acht IO-Link-Ports und bindet damit bis zu acht Geräte über eine einzelne Verbindung an die Steuerung an. Schließe ich dagegen acht Sensoren über SPE an, manage ich acht einzelne Steuerungsverbindungen. Da jede Verbindung eingerichtet und verwaltet werden muss, werden dazu auch Ressourcen an Speicher und Rechenleistung belegt. SPE wird kein Ersatz, sondern eine Ergänzung für IO-Link sein. Wir sind davon überzeugt, das SPE seinen Platz finden wird als Ergänzung der heute verfügbaren Technologien.
Seidel-Sridhavan: IO-Link als Technologie bietet ein erhebliches Potenzial, um auch neue Geschäftsfelder zu erschließen, doch die Performance ist begrenzt. Geräte, die mehr Datenrate erfordern, stehen bei IO-Link nicht im Fokus. Die Message ist klar, IO-Link+ ist eine Erweiterung, nicht der Nachfolger von IO-Link.
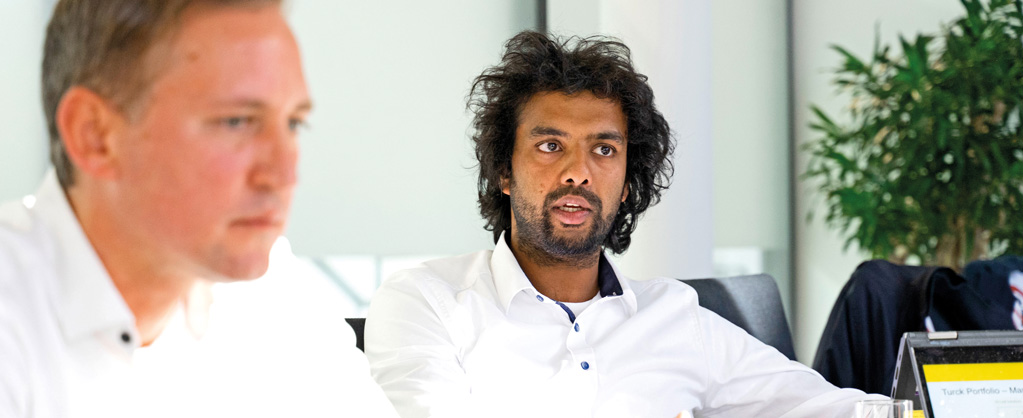
Welche Bedeutung misst Turck als Safety-Anbieter dem Thema IO-Link Safety bei?
Buda: Wir beobachten den Markt sehr genau. Turck bietet verschiedene Safety-Produkte, gerade im IP67-Bereich – Profisafe- und hybride Geräte, die Safety-Kanäle und IO-Link kombinieren, mit integrierter Abschaltfunktion, mit der sich Aktorik sicher abschalten lässt. Das entspricht aber nicht dem IO-Link-Safety-Protokoll. Die Technologie als solches ist interessant und wird IO-Link weiter voranbringen. Wir betrachten IO-Link Safety auch als einen interessanten Ansatz, weil gerade der Safety-Bereich geprägt ist von proprietären Sensor- und Aktor-Systemen. IO-Link Safety ist der erste harmonisierte Standard auf der unteren Ebene. Damit werden wir ein heterogenes Anbieterfeld für sichere Schalter und Sensoren bekommen, die auch an Master verschiedener Hersteller anschließbar sind.
Seidel-Sridhavan: Die meisten Hersteller haben in den letzten Jahren Geräte für den sicheren Bereich entwickelt, die IO-Link mit Profisafe verknüpfen. Da es sich dabei um zwei Konzepte handelt, hat das die IO-Link-Community nicht unterstützt. IO-Link Safety ist unabhängig von Profinet, Ethercat oder Ethernet/IP. Bei der PNO sind bereits Spezifikationen ausgearbeitet, wie IO-Link-Safety in Profinet integriert werden kann, und die anderen Organisationen werden sicher folgen. Wichtig ist, dass sich die Hersteller von Sicherheitssensoren und Aktoren auf einen Standard fokussieren. Eine Türzuhaltung beispielsweise erfordert bisher einen hohen Aufwand bei der Verdrahtung. IO-Link-Safety mit seiner bidirektionalen Kommunikation würde da erhebliche Vorteile bringen.
Autor | Das Gespräch führte Andreas Gees, Redakteur der Fachzeitschrift elektroAutomation
- Technologien
- Externe Partner
Land wählen
Turck weltweit